Maintaining the Cold Chain
PDA's Technical Report No. 39 provides guidance for protecting temperature-sensitive products.
Drugs shipped by truck, train, ship, or aircraft can be subjected to temperatures ranging from far below zero to well above 100 °F, sometimes during the same trip. Exposure to these extremes can be disastrous for temperature-sensitive products. In less severe cases, shelf life can be shortened. In worst-case scenarios, product can be ruined, resulting in losses that can add up to hundreds of thousands of dollars.
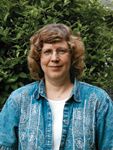
Hallie Forcinio
To help pharmaceutical manufacturers protect temperature-sensitive products during shipment, the Parenteral Drug Association (Bethesda, MD, www.pda.org) has published a guidance document drafted by its Cold Chain Management Task Force and reviewed by technical experts from the industry. Several years in the making, "Technical Report No. 39: Cold Chain Guidance for Medicinal Products: Maintaining the Quality of Temperature-Sensitive Medicinal Products through the Transportation Environment" discusses how to develop protective packages and systems to provide "thermally controlled transportation" (1). The guidance also aligns with the Center for Drug Evaluation and Research's (Bethesda, MD, www.fda.gov) "General Principles of Process Validation: Component Qualification (CQ), Operating Qualification (OQ), and Performance Qualification (PQ)."
Stability studies. Determining how to protect products depends heavily on stability studies. Actual studies are needed because "Long-term storage or label storage temperatures may be different from short-term shipping/distribution temperatures" (1). Three types of studies should be undertaken to address temperature control issues: long-term, accelerated, and temperature excursion. Temperature excursion studies are particularly important because it's not uncommon for shipments to be exposed to conditions outside anticipated extremes because of weather, delays, equipment malfunctions, mishandling, or other causes.
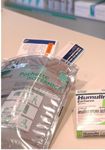
Multiple layers of CrioMED Plus insulated bag protect product inside from temperature extremes.
All levels of packaging from primary container–closures to distribution packaging affect the product's thermal stability and should be included in the testing program. In fact, "The more empty space within the secondary package not utilized by the thermal mass of the product, the more difficult it is to control the system thermally" (1).
Developing a protective system. The development of a thermally protective system begins with the creation of a functional requirements document and the specification of components such as insulated containers and refrigerants. The functional requirements document includes the critical parameters related to the packaging and transport systems such as the types of vehicle, routes, trip duration, product stability, likely temperature range of exposure, and packaging. The component specification is a detailed description of requirements for features such as material composition, mechanical characteristics, dimensions, printing, storage, sampling, weight, insulation, calibration limits, fragility limits, and shock and vibration limits.
Design testing is the next step. "The outcome of design testing assures a high confidence for successful operational qualification of a specific package or system," the report explains (1).
Then, qualification testing is "performed using the designated configuration to provide assurance that product quality is maintained during transport." Both design and qualification testing results should be documented in a formal report (1).
Once testing is completed successfully, process implementation occurs. Provisions also should be made for training, quality assurance, maintenance of appropriate records for regulatory inspectors, and periodic reevaluation. The latter is necessary because "Even a qualified process is subject to change over time" (1).
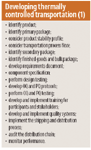
Developing thermally controlled transportation (1)
Additional resources. Technical Report No. 39 also includes a list of references, a glossary of terms, an appendix describing International Conference on Harmonization (Geneva, Switzerland, www.ich.org) and World Health Organization (Geneva, Switzerland, www.who.int/en/) stability tests, and an example of a study design for a refrigerated product. Finally, a sample transportation control strategy document outlines the effect of various temperature excursions on a particular product and advises whether it can still be used and to what degree the shelf life has been affected.
Regulators also continue to work on cold chain management. Health Canada (Ottawa, ON, Canada www.hc-sc.gc.ca/index_e.html) issued the final version of its guidance document, "Guidelines for Temperature Control of Drug Products during Storage and Transportation," in October 2005 (2). It contains specific recommendations for production transportation, containers, and container labeling.
Cold chain management tools
Drug makers have many options to help ensure temperature-sensitive products move through the supply chain under appropriate conditions, including time-temperature indicators, data loggers, radio frequency identification (RFID) technology, and insulated shippers and refrigerants. Several products and vendors have come to light since previous articles on this topic appeared (3, 4).
Pressure-sensitive temperature indicator labels integrate phase-change chemistry to irreversibly change color and provide a visual indication that thermal parameters have been exceeded. Customized designs can be set to thresholds from 0 to 200 °C and are produced in an ISO-9001:2000-certified, FDA-registered facility. Labels can be supplied on rolls for automated application (Customized Irreversible temperature indicators, American Thermal Instruments, Inc., Beavercreek, OH, www.americanthermal.com). The company also offers a stock-freeze indicator (Freeze√ Freeze Indicator).
A disposable, electronic temperature indicator, developed by a supplier of refrigerants and insulated shipping containers, reads "OK" if a shipment has not been temperature abused in transit. Each unit is programmed to the customer's time–temperature requirements and then tested to make sure it is reading accurately. The battery-powered unit weighs only 0.5 oz and can function as long as two years after activation. Double-sided tape affixes the indicator to the product being stored or shipped (KoolWatch electronic temperature indicator, Cold Chain Technologies, formerly FDC Packaging, Holliston, MA, www.coldchaintech.com).
An advanced data-logging system incorporates monitoring and alarming software to provide deviations alerts. Rather than recording data at a single location like traditional monitoring systems, the software monitors temperature and humidity using data loggers arranged in a network throughout a shipment or site. The software connects to the independent data loggers and provides a centralized way to view the information. Distributing data-recording responsibilities among multiple sensors also enhances system reliability. If one sensor fails, others continue monitoring conditions (viewLinc Enterprise monitoring and alarming software, Veriteq, Richmond, BC, Canada, www.veriteq.com).
Temperature monitoring and logging also can be accomplished with RFID labels. A credit-card–size "smart" label with a 13.56-MHz RFID chip and paper-thin battery provides 2 kB of read-and-write memory to record data. Available in disposable and reusable designs, labels can withstand temperatures from –15 °C to +50 °C. Labels can be set to monitor and log temperatures automatically at programmed intervals ranging from 10 s to 16 h. On-chip intelligence optimizes memory usage by only storing values outside the two temperature limits established by the user plus the minimum and maximum temperatures experienced. Data are retrieved via an RFID reader (KSW–TempSens smart label with temperature monitoring function, KSW-Microtec, Dresden, Germany, www.ksw-microtec.com). To test the system, the company offers a demonstration kit that includes 10 smart labels, a reader with USB port, Microsoft Windows-compatible software, and a command set and user manual.
Another RFID-based system tags shipments of refrigerated goods and begins monitoring with the push of a button. In the event of a temperature excursion, the tag displays a warning light. The custom-programmable tags include both disposable and reusable models (LogIC active RFID sensors, American Thermal Instruments).
Whether time–temperature indicators, data loggers, or RFID technology are used, it is likely that insulated shippers and refrigerants will be necessary to maintain products at the proper temperature.
A supplier of insulated shipping containers, refrigerants, and temperature indicators has assembled a collection of products suitable for pharmaceutical packaging. The firm not only stocks multiple sizes of expanded polystyrene (EPS) shippers, but also offers urethane foam shippers that offer twice the R, or insulating value/in., compared with EPS and, thus, may require less refrigerant (Cold Ice, Inc., Oakland, CA, www.coldice.com).
Nestable insulated shippers stack inside each other to reduce the space occupied in shipping and storage. A larger top half provides space for refrigerants and provides optimum placement for chill penetration. Eight stock sizes permit the shipper to be matched to the product and the environmental conditions it will encounter (ThermoChill nestable overnight insulated containers, PolarTech, Genoa, IL, www.polar-tech.com).
For pallet-size loads, a modular system offers a mix-and-match array of refrigerants, blankets, and bags to deliver ultimate protection (ThermoChill modular component perishable pallet system, PolarTech).
Reusable, iceless containers maintain specific refrigerated or below-freezing temperatures during transportation and storage regardless of hotter or colder ambient conditions. Designed for the military to protect blood shipments and developed in conjunction with the Walter Reed Army Institute of Research (Silver Spring, MD, http://wrair-www.army.mil/), the concept won an Army Greatest Invention award in 2004. The top-opening corrugated case with two side flaps and tab-lock top flap houses vacuum insulated panels on all six sides plus a thermal isolation chamber made up of hinged hollow panels filled with a phase change liquid. Hinged panels make it possible to flatten the chamber for more compact chilling. Insulated shipper weighs less than 30 pounds. One style of shipper maintains contents between 1 and 10 °C for at least 60 hours. Frozen products can be held at –18 °C for at least 48 hours (Golden Hour 4 °C Shipping Container and Golden Hour Minus 20 °C Shipping Container, Minnesota Thermal Science, LLC, Plymouth, MN, www.mnthermalscience.com). Shippers can be designed in various sizes and maintain other temperatures. Two other stock products maintain a temperature of 22 °C or –50 °C.
New to the US market is a flexible insulated packaging specialist headquartered in Italy. Already in use by several vaccine makers, the multilayer metallized film–foam–opaque film bags can be customized with full-color printing in as many as 10 colors. Bags are available in two stock sizes (20 X 25 cm and 30 X 35 cm) as well as custom dimensions and can incorporate airtight reclosable zippers, an integral refrigerant and die-cut or molded handles (CrioMED Plus insulated pharmacy bag, Imball Center S.r.l.-Termika.us, Roswell, GA, www.termika.us).
A controlled-temperature system consisting of a cooling device, shipping carton, and vacuum-insulated panels maintains products at 2–8 °C. Relying on evaporative cooling technology to pull heat away from the product, the self-contained package incorporates a push-button–activated cooling device in the lid, thereby eliminating the need for refrigerants and reducing the size of the package by as much as 70% compared with traditional insulated shippers using EPS foam and gel packs. With weight savings also likely, the system tends to lower shipping costs (NanoCool system, NanoCool LLC, Charleston, SC, www.nanocool.com).
Some controlled-temperature shipping systems are specifically designed for certain modes of transportation. A system that protects temperature-sensitive air shipments won a Cold Chain Management Excellence Award in October 2005 from the International Quality & Productivity Center (New York, NY, www.iqpc.com). The reusable containers, which are available in three sizes from a Sweden-based company, feature active temperature control (Envirotainer, Envirotainer Inc., Irving, TX, www.envirotainer.com).
Some suppliers of cold chain management products also provide testing, design, and certification services. Temperature studies can be done with dry ice, gel packs, or shipment simulation (temperature testing, Therapak, Irwindale, CA, www.therapak.com; package qualification and testing, Cold Chain Technologies' Cold Chain Laboratories; cold-chain management validation and qualification services, Envirotainer Inc.; and custom design services, Cold Ice, Inc.).
Hallie Forcinio is Pharmaceutical Technology's Packaging Forum editor, 4708 Morningside Drive, Cleveland, OH 44109, tel. 216.351.5824, fax 216.351.5684, editorhal@cs.com
References
1. Parenteral Drug Association, "Technical Report No. 39: Cold Chain Guidance for Medicinal Products: Maintaining the Quality of Temperature-Sensitive Medicinal Products through the Transportation Environment," J. Pharma. Sci. Technol. 59 (S-3), (2005).
2. Health Canada, "Guidelines for Temperature Control of Drug Products during Storage and Transportation (GUIDE-0069)," (Health Canada, Ottowa, ON, Canada, 2005), http://www.hc-sc.gc.ca/dhp-mps/compli-conform/gmp-bpf/docs/gui-0069_temp_control_dproducts_storage_transportation_ltr-doc_e.html, accessed Feb. 15, 2006.
3. H. Forcinio, "Packaging Helps Protect Temperature-Sensitive Products," Pharm. Technol. 28 (30), 36–42 (2004).
4. H. Forcinio, "Cold Chain Concerns," Pharm. Technol. 29 (4), 44–50 (2005).
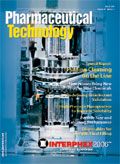
Drug Solutions Podcast: A Closer Look at mRNA in Oncology and Vaccines
April 30th 2024In this episode fo the Drug Solutions Podcast, etherna’s vice-president of Technology and Innovation, Stefaan De Koker, discusses the merits and challenges of using mRNA as the foundation for therapeutics in oncology as well as for vaccines.